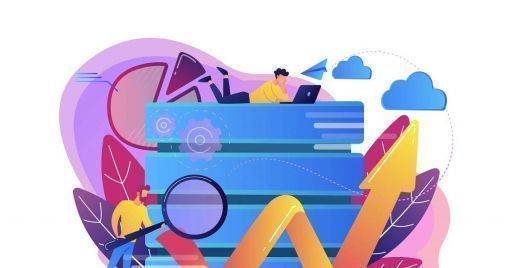
Using data to improve occupational safety training
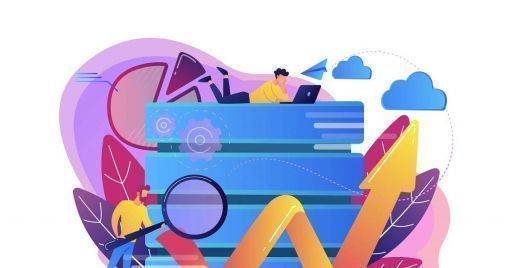
How can eLearning and data analysis be used to analyse the effects of training on the frequency and severity of occupational accidents?
Occupational safety training is a fundamental activity to prevent accidents in the workplace and protect the health of workers. The objective of this training is to provide workers with the necessary skills to identify hazards in the workplace and take appropriate precautions to avoid accidents.
In the past, occupational safety training was mainly based on participation in classroom lectures and field training sessions. Thanks to the growth of eLearning, occupational safety training has become more accessible, flexible and interactive.
eLearning offers numerous advantages in occupational safety training, such as ubiquitous accessibility, personalization of the learning path, interactivity, traceability and constant updating of content. These benefits of eLearning have become even more important during the Covid-19 pandemic, when face-to-face learning became problematic.
Occupational safety data and analysis
Workplace safety is a very important issue, and because of this, companies are required to constantly monitor data related to the safety of their workers. Occupational safety data can include a variety of information such as the number of accidents and their severity, divided by type of injury; the causes that produced them and the type of activities and work most involved; the body parts injured; and the duration of absence from work due to accidents.
Analysis of occupational safety data is a key tool for improving workplace safety. The primary purpose of these analyses is to identify the causes of accidents so that the effectiveness of preventive measures taken can be evaluated and strategies developed to improve workplace safety.
For example, a quantitative approach can be used to reveal what times of day or what type of machinery generates most workplace accidents. This information can help the company improve surveillance and take specific preventive measures to reduce the risk of accidents.
In addition, data analysis can help companies identify which employees are most at risk of suffering workplace accidents and take preventive measures specifically for them. If the assessments show a significant correlation between seniority and type of injury, human resources, in consultation with those involved in corporate safety, may take different actions. For example, one case is whether one type of injury is more likely to affect new hires. In this case, it could be assumed that the initial training is not sufficient and that the new staff does not yet have the wealth of acquired experience that would enable them to automatically follow the correct procedures. Conversely, if employees with greater seniority were more prone to a given risk, it might be necessary to consider whether, in addition to appropriate refresher courses on any new technologies or tools adopted, it would be appropriate to consider a change in the duties of the individuals in order to take preventive measures specific to them, such as reducing workloads.
In summary, the analysis of occupational safety data is an important tool for improving workplace safety. The data can provide valuable information about the causes of accidents and the areas where they occur most frequently, while their analysis can help companies identify the employees most at risk and take preventive measures specifically for them.
How eLearning can improve occupational safety training
eLearning is an essential technology for providing occupational safety training. Examples of eLearning training programs for occupational safety include online courses, webinars, video tutorials, and interactive quizzes. These programs can be supplemented with occupational safety data and analysis to create a more comprehensive and customized training system. Some of the benefits of its use can be summarized as follows:
- Flexibility
- Upgrading
- Costs
- Customization
eLearning allows workers to take on-the-job safety training anytime, anywhere, without having to worry about travel or being present in the classroom. This allows that organizational flexibility that is extremely useful for companies to make training truly "on" the job: by reducing the time distance between training and the flow of activities in each task, both the worker and his or her supervisors can apply safety procedures at work.
eLearning makes it possible to update occupational safety training courses quickly and efficiently, ensuring that workers always receive the most up-to-date and relevant information. A change in regulations, changing environmental hazard conditions, or new types of processing and machinery used may require additional updates, for which eLearning training offerings may have the required content. eLearning is often cheaper than traditional classroom training.
eLearning is often cheaper than traditional classroom training. The very cost structure of providers changes with the use of this technology: from a set of variable cost items -classrooms, equipment and teaching staff- that are repeated with each course delivered, there is a shift to fixed costs -content production- that allow individual lessons to be replicated at progressively lower costs. This is the effect of economies of scale, which make it cheaper to provide the same service the more you offer. On the client company side, eLearning saves on worker travel costs and organizational logistics.
Finally, the opportunity to create training paths tailored to the needs of each task and process is another important benefit. For example, an occupational safety training course for workers operating in a machine shop will be different from one for workers operating in a server room. Safety training courses that are designed in a modular format can be recombined according to different needs: a core will be common to all, such as first safety procedures, to name one; other modules will be specific to the industry in which the company operates or the type of processing and machinery used.
This approach also allows for the eventual progression of the employee who is tasked with or intends to take on roles of greater responsibility. Indeed, safety management in the company is composed of several figures, each important and with specific tasks:
- The Safety Prevention and Protection Manager
- The Workers' Safety Representative
- The fire prevention officer
- The First Aid Officer
Each of these categories is required to acquire specific skills useful to their role.
Using data to improve occupational safety training with eLearning
The use of data in occupational safety training can greatly improve the effectiveness of the training itself. Data can be used to tailor training to the specific needs of workers and departments. In addition, the use of data analysis tools can help identify major risk areas and develop specific training programs for those areas.
For example, the use of accident and injury data can help identify major risk areas. Data on employees who suffer workplace injuries or accidents can be used to develop training programs specifically for those employees, focusing on the skills and knowledge needed to reduce the risk of workplace injuries.
In summary, using data and data analysis tools in occupational safety training with eLearning can help tailor training to the specific needs of workers and departments, identify areas of greatest risk, and develop specific training programs to reduce risk in those areas.
Conclusions
In summary, eLearning can be a valuable tool for improving occupational safety training. The use of data can help companies tailor their training programs and adapt them to the specific needs of workers. Data analysis can be used to identify areas where workers may be most at risk and create specific training programs to mitigate these risks.
To successfully implement workplace safety training programs based on eLearning and data analytics, companies need to consider several factors. First, it is important for companies to invest in data analysis tools to monitor workplace safety and gather relevant information. This information will need to be studied and evaluated by knowledgeable people who can perform quantitative analysis to link different events together and find out whether there are cause and effect relationships between them, such as there might be between the speed of a process and the frequency of accidents or between employee experience and the type of accident.
eLearning platforms that allow to extract organized data on courses and attendees can be incorporated into this quantitative approach to workplace safety. The search for correlations can work two ways: establishing a link between the performance of attendees and the type of injuries and accidents that occurred before and after the course; and deciding for the administration of additional courses to reduce the likelihood and frequency of these accidents and injuries.
Using data to improve occupational safety training with eLearning can help companies reduce risks and improve worker safety. By investing in data analysis tools and professional eLearning platforms, companies can create effective, customized training programs that help protect workers in the workplace.
Did you like this article? Sign up for the newsletter and receive weekly news!
Subscribe to NewsletterComments:
No comments are in yet. You be the first to comment on this article!